Planowanie i realizacja relokacji maszyn - o co w niej chodzi?
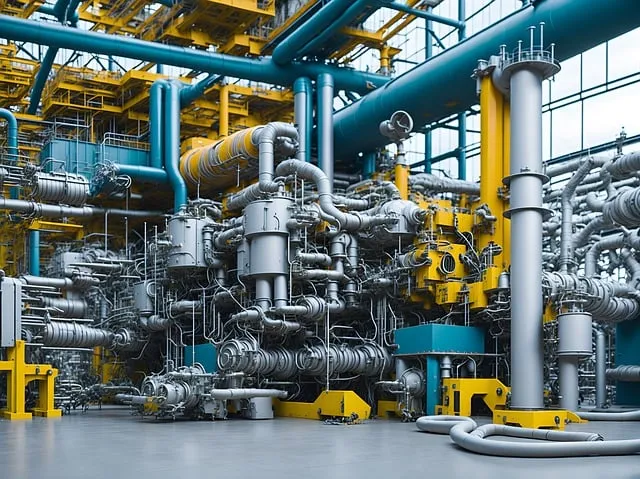
Relokacja maszyn to proces, który wymaga precyzyjnego planowania, zaawansowanych umiejętności technicznych oraz doświadczenia w zarządzaniu skomplikowanymi projektami. Niezależnie od tego, czy chodzi o wewnętrzne przestawienie urządzeń w ramach jednego zakładu, czy przeniesienie maszyn do zupełnie nowej lokalizacji, każdy etap relokacji musi być szczegółowo zaplanowany, aby zminimalizować ryzyko przestojów, uszkodzeń sprzętu i dodatkowych kosztów.
Czym jednak dokładnie jest relokacja maszyn i jakie kroki obejmuje? Poniżej przyjrzymy się szczegółowo procesowi planowania i realizacji przenoszenia urządzeń przemysłowych.
Czym dokładnie jest relokacja maszyn?
Relokacje maszyn to proces polegający na przeniesieniu urządzeń przemysłowych z jednej lokalizacji do innej, który może odbywać się zarówno w obrębie tego samego zakładu (relokacja wewnętrzna), jak i między różnymi obiektami, a nawet krajami (relokacja zewnętrzna). Obejmuje szereg działań, takich jak demontaż maszyn, ich odpowiednie zabezpieczenie, transport, a następnie ponowny montaż i uruchomienie w nowym miejscu. Relokacja maszyn jest często konieczna w sytuacjach, gdy firma reorganizuje procesy produkcyjne, modernizuje zakład, optymalizuje wykorzystanie przestrzeni lub przenosi działalność do bardziej korzystnej lokalizacji.
To kompleksowe przedsięwzięcie wymaga precyzyjnego planowania, odpowiedniego sprzętu oraz wiedzy technicznej, aby zapewnić bezpieczne przeniesienie urządzeń i ich pełną funkcjonalność po zakończeniu procesu. Relokacja maszyn nie ogranicza się tylko do fizycznego transportu jest to strategiczne działanie, które może znacząco wpłynąć na efektywność operacyjną przedsiębiorstwa i jego konkurencyjność na rynku.
Tworzenie planu relokacji maszyn
Tworzenie planu relokacji maszyn to etap, który zapewnia płynny przebieg całego procesu i minimalizuje ryzyko nieprzewidzianych problemów. Jednym z podstawowych elementów planowania jest opracowanie szczegółowego harmonogramu działań, który uwzględnia kolejne etapy, takie jak demontaż, transport, ponowny montaż i uruchomienie maszyn. Harmonogram powinien być dostosowany do specyfiki zakładu i produkcji, tak aby zminimalizować przestoje i ograniczyć wpływ relokacji na bieżącą działalność przedsiębiorstwa.
Równie ważna jest ocena ryzyka, która pozwala przewidzieć potencjalne problemy, takie jak uszkodzenia sprzętu, opóźnienia transportowe czy zakłócenia w harmonogramie produkcji. Dzięki tej analizie można opracować strategie zapobiegawcze i przygotować odpowiednie środki zaradcze. Istotnym elementem tworzenia planu jest także koordynacja zespołu odpowiedzialnego za relokację. Jasne przydzielenie zadań, efektywna komunikacja i współpraca między działami technicznymi, logistycznymi i kierownictwem projektu są niezbędne, aby zapewnić, że wszystkie działania przebiegają zgodnie z planem.
Zapewnienie ciągłości produkcji
Zapewnienie ciągłości produkcji podczas relokacji maszyn to jedno z najważniejszych wyzwań, przed którymi stają przedsiębiorstwa. Ważnym elementem jest szczegółowe zaplanowanie działań, które pozwala ograniczyć przestoje do minimum. W tym celu należy opracować harmonogram prac tak, aby przenoszenie maszyn odbywało się etapami, umożliwiając jednoczesne utrzymanie części procesów produkcyjnych. Alternatywnie, warto rozważyć wprowadzenie tymczasowych rozwiązań, takich jak przeniesienie części produkcji na inne linie lub wykorzystanie dodatkowych zasobów, które pozwolą na realizację najważniejszych zadań operacyjnych.
Równie istotne jest wcześniejsze zabezpieczenie odpowiednich zapasów materiałów i produktów, które mogą pokryć ewentualne opóźnienia w procesie produkcyjnym. Dobrą praktyką jest również prowadzenie regularnej komunikacji z zespołem i partnerami biznesowymi, aby wszyscy byli świadomi harmonogramu oraz ewentualnych zmian w procesach. Dzięki odpowiedniemu zarządzaniu relokacją można zminimalizować ryzyko przerw w działalności przedsiębiorstwa, jednocześnie maksymalizując korzyści płynące z przeniesienia maszyn i ich lepszego dopasowania do potrzeb produkcyjnych.
Autor: Materiał partnera